Flow Level Pressure Temperature Control Bench
Categories: Lab EquipmentFlow Level Pressure Temperature Control Bench Flow Level Pressure Temperature Control Bench Control of water levels in loop. Control of water flow by winnowing. Control of water pressure by win...
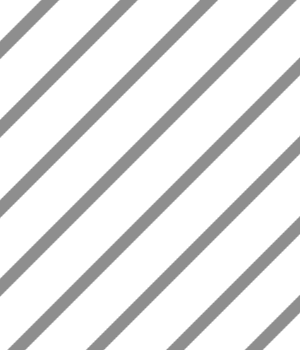
Product
Description
Flow Level Pressure Temperature Control Bench
Flow Level Pressure Temperature Control Bench- Control of water levels in loop.
- Control of water flow by winnowing.
- Control of water pressure by winnowing.
- Control of water temperature, (piloting resistive charges per static power unit).
- Control of water temperature with cascade on the flow.
Teaching Objectives of Flow Level Pressure Temperature Control Bench
- Study of the closed loop syste.
- Stability conditions.
- Response to a level instruction.
- Influence of the parameters of control and the algorithm setting (TOR, P, PI, or PID) on the results.
- Study of an open loop system.
- Study of the characteristic curves of the system.
- Study of a cascade control system
Technical Specifications of Flow Level Pressure Temperature Control Bench
- A supply tank of 50 liters out of PVC, with taping and overflow.
- A Altuglass column high 1200 mm, diam. 200 mm with overflow and drain tap.
- A centrifugal pump, 380 V three phases.
- A master regulator with universal input, output 4-20 mA and a slave regulator, regulation algorithm P, PI, PID, PD + MR. function auto/manual – auto-adaptative with double display measure/instruction.
- Proportional pneumatic valve, with positioning.
- I/P Converter.
- Pressure control by pressure transmitter (output 4-20 mA).
- Electronic flowmeter (output 4-20 mA).
- 4 rotary flowmeters with tap.
- Level measurement by pressure transmitter (4-20 mA) placed at the bottom of an Altuglass water column with overflow and drain valve.
- Immersion heater with thermostat.
- 2 temperature probes Pt 100 ohms with transmitter 4/20 mA.
- An electric cabinet including: the regulators, the protection of the pump and its command Wiring of the closed loop thanks safe jacks and wires.
- Mounted on a stainless steel frame with aluminium nut.
- 5 Process are possible.
- 1 - level control.
- Actuator : pneumatic valve.
- Sensor : pressure transmitter.
- Disruption : leak on the pipe , leak under the column.
- 2 – Flow control.
- Actuator : pneumatic valve.
- Sensor : Electronic flowmeter.
- Disruption : leak on the pipe
- Actuator: pneumatic valve.
- Sensor: pressure transmitter.
- Disruption: leak on the pipe.
- Actuator: immersion heater.
- Sensor: temperature probe.
- Disruption: by provision of cold water.
- Actuator: pneumatic valve.
- Sensor: temperature probe at the output of the heater and electronic flowmeter.
- Disruption: leak on the pipe, variation of the heater’s power
Dimensions and weight
- 1500 x 800 x 2100 mm.
- Weight: about 150 kg.
Essential requirements
- Electric power supply: 7 kW 380 V triphase.
- Compressed air: 6Nl/h, 6 bars.
Services nécessaires
- Consommation 0,37 kW – 220 V monophasé.
- Documentation pédagogique et technique.
quick overview :
Flow Level Pressure Temperature Control Bench
Flow Level Pressure Temperature Control Bench- Control of water levels in loop.
- Control of water flow by winnowing.
- Control of water pressure by winnowing.
- Control of water temperature, (piloting resistive charges per static power unit).
- Control of water temperature with cascade on the flow.
Teaching Objectives of Flow Level Pressure Temperature Control Bench
- Study of the closed loop syste.
- Stability conditions.
- Response to a level instruction.
- Influence of the parameters of control and the algorithm setting (TOR, P, PI, or PID) on the results.
- Study of an open loop system.
- Study of the characteristic curves of the system.
- Study of a cascade control system
Technical Specifications of Flow Level Pressure Temperature Control Bench
- A supply tank of 50 liters out of PVC, with taping and overflow.
- A Altuglass column high 1200 mm, diam. 200 mm with overflow and drain tap.
- A centrifugal pump, 380 V three phases.
- A master regulator with universal input, output 4-20 mA and a slave regulator, regulation algorithm P, PI, PID, PD + MR. function auto/manual – auto-adaptative with double display measure/instruction.
- Proportional pneumatic valve, with positioning.
- I/P Converter.
- Pressure control by pressure transmitter (output 4-20 mA).
- Electronic flowmeter (output 4-20 mA).
- 4 rotary flowmeters with tap.
- Level measurement by pressure transmitter (4-20 mA) placed at the bottom of an Altuglass water column with overflow and drain valve.
- Immersion heater with thermostat.
- 2 temperature probes Pt 100 ohms with transmitter 4/20 mA.
- An electric cabinet including: the regulators, the protection of the pump and its command Wiring of the closed loop thanks safe jacks and wires.
- Mounted on a stainless steel frame with aluminium nut.
- 5 Process are possible.
- 1 - level control.
- Actuator : pneumatic valve.
- Sensor : pressure transmitter.
- Disruption : leak on the pipe , leak under the column.
- 2 – Flow control.
- Actuator : pneumatic valve.
- Sensor : Electronic flowmeter.
- Disruption : leak on the pipe
- Actuator: pneumatic valve.
- Sensor: pressure transmitter.
- Disruption: leak on the pipe.
- Actuator: immersion heater.
- Sensor: temperature probe.
- Disruption: by provision of cold water.
- Actuator: pneumatic valve.
- Sensor: temperature probe at the output of the heater and electronic flowmeter.
- Disruption: leak on the pipe, variation of the heater’s power
Dimensions and weight
- 1500 x 800 x 2100 mm.
- Weight: about 150 kg.
Essential requirements
- Electric power supply: 7 kW 380 V triphase.
- Compressed air: 6Nl/h, 6 bars.
Services nécessaires
- Consommation 0,37 kW – 220 V monophasé.
- Documentation pédagogique et technique.
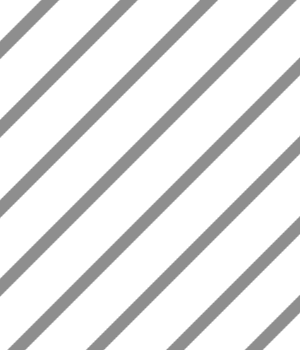
Product
Reviews
add Review
reviews
No Review Yet.
Product
Reviews
add Review
reviews
No Review Yet.